
Diferencias entre un PLC y un DSC: Características y aplicaciones
En este artículo exploramos las diferencias clave entre los Controladores Lógicos Programables (PLC) y los Controladores de Sistemas Distribuidos (DSC), detallando sus características, aplicaciones y modelos destacados de Siemens como el SIMATIC S7-1200 y el SIMATIC PCS 7. Descubra cuándo es más adecuado usar cada uno y cómo estas tecnologías pueden optimizar la automatización industrial.
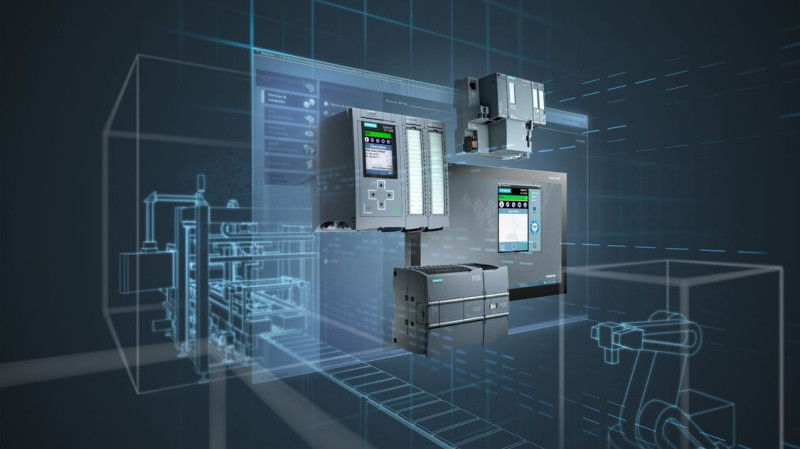
En el ámbito de la automatización industrial, dos de los sistemas más importantes son el PLC (Controlador Lógico Programable) y el DSC (Controlador de Sistemas Distribuidos). Aunque ambos desempeñan funciones cruciales en el control y supervisión de procesos industriales, existen diferencias clave en su diseño, aplicación y características. En esta entrada del blog, exploraremos estas diferencias, analizaremos cuándo es más adecuado utilizar uno u otro, y revisaremos algunos de los modelos que Siemens ofrece en cada categoría.
¿Qué es un PLC?
Un Controlador Lógico Programable (PLC) es un dispositivo electrónico diseñado para automatizar procesos industriales mediante la ejecución de programas lógicos. Los PLCs son esenciales en la automatización de maquinaria, líneas de producción y otros procesos que requieren un control preciso y repetitivo. Entre sus principales características destacan:
- Flexibilidad y Adaptabilidad: Los PLCs pueden ser reprogramados fácilmente para adaptarse a cambios en el proceso.
- Confiabilidad: Están diseñados para operar en ambientes industriales hostiles, con alta resistencia a vibraciones, temperaturas extremas y humedad.
- Tiempo Real: Los PLCs operan en tiempo real, lo que permite un control inmediato y preciso de los procesos.
- Interconectividad: Son capaces de comunicarse con otros dispositivos y sistemas mediante protocolos industriales estándar como Profibus, Profinet, y Ethernet/IP.
¿Qué es un DSC?
Un Controlador de Sistemas Distribuidos (DSC) es un sistema de control industrial utilizado para gestionar y supervisar procesos complejos y distribuidos geográficamente. Los DSCs son ideales para aplicaciones en las que se requiere el control y monitoreo de múltiples procesos en tiempo real desde una ubicación central. Sus principales características incluyen:
- Escalabilidad: Los DSCs pueden gestionar una gran cantidad de entradas y salidas, y son fácilmente escalables para adaptarse a la expansión del proceso.
- Integración: Permiten la integración de varios subsistemas y dispositivos de diferentes fabricantes, facilitando una gestión unificada del proceso.
- Redundancia y Seguridad: Ofrecen altos niveles de redundancia y seguridad, minimizando el riesgo de fallos del sistema.
- Supervisión Centralizada: Proporcionan herramientas avanzadas de visualización y análisis de datos para una supervisión centralizada y eficiente del proceso.
Diferencias Principales entre PLC y DSC
1. Arquitectura del Sistema:
- PLC: Utiliza una arquitectura centralizada donde un único controlador gestiona todas las entradas y salidas. Ideal para aplicaciones de control directo de máquinas y procesos específicos.
- DSC: Emplea una arquitectura distribuida que permite controlar y supervisar múltiples subsistemas y procesos desde un centro de control. Es adecuado para procesos industriales complejos y distribuidos.
2. Aplicaciones:
- PLC: Comúnmente utilizado en manufactura, líneas de producción, control de maquinaria, y aplicaciones donde se requiere una respuesta rápida y precisa.
- DSC: Utilizado en industrias como petroquímica, generación de energía, tratamiento de agua, y otras aplicaciones donde el control y monitoreo de procesos distribuidos es crítico.
3. Escalabilidad y Complejidad:
- PLC: Mejor para aplicaciones de menor escala con requerimientos de control directo y específico.
- DSC: Adecuado para aplicaciones de gran escala que requieren un alto grado de integración y coordinación entre diferentes subsistemas.
Aplicaciones Adecuadas
- Usos Ideales de PLC:
- Líneas de ensamblaje automotriz
- Sistemas de transporte y cintas transportadoras
- Máquinas de envasado
- Control de bombas y compresores
- Usos Ideales de DSC:
- Plantas de refinación de petróleo
- Centrales eléctricas
- Plantas de tratamiento de aguas residuales
- Industria química.
Modelos de Siemens
Siemens ofrece una amplia gama de PLCs y DSCs adaptados a diferentes necesidades industriales. A continuación, revisamos algunos de los modelos más destacados:
- PLCs de Siemens:
- SIMATIC S7-1200: Un PLC modular compacto, ideal para tareas de automatización de pequeña a mediana escala. Ofrece un excelente rendimiento, flexibilidad y facilidad de uso.
- SIMATIC S7-1500: Diseñado para aplicaciones de alta exigencia, ofrece capacidades avanzadas de procesamiento, diagnóstico y comunicación. Es altamente escalable y adecuado para aplicaciones complejas.
- DSCs de Siemens:
- SIMATIC PCS 7: Este sistema de control distribuido es altamente escalable y flexible, adecuado para aplicaciones en la industria de procesos. Ofrece una integración completa de control y supervisión, proporcionando herramientas avanzadas de diagnóstico y análisis.
- SPPA-T3000: Utilizado principalmente en la generación de energía, este DSC ofrece una plataforma de control unificada para la supervisión y control de plantas eléctricas.
Conclusión
La elección entre un PLC y un DSC depende en gran medida de la naturaleza del proceso industrial a controlar. Los PLCs son ideales para aplicaciones que requieren control directo, repetitivo y de alta velocidad, mientras que los DSCs son más adecuados para procesos distribuidos y complejos que requieren una supervisión centralizada y un alto nivel de integración.
Siemens, con su amplia gama de soluciones en ambos ámbitos, proporciona las herramientas necesarias para optimizar la eficiencia y fiabilidad de los procesos industriales. La selección adecuada del sistema de control no solo mejora la productividad, sino que también garantiza la flexibilidad y escalabilidad para futuras expansiones y mejoras.
Escribe un comentario